Slide title
Write your caption hereButtonSlide title
Write your caption hereButtonSlide title
Write your caption hereButtonSlide title
Write your caption hereButtonSlide title
Write your caption hereButton
Blog
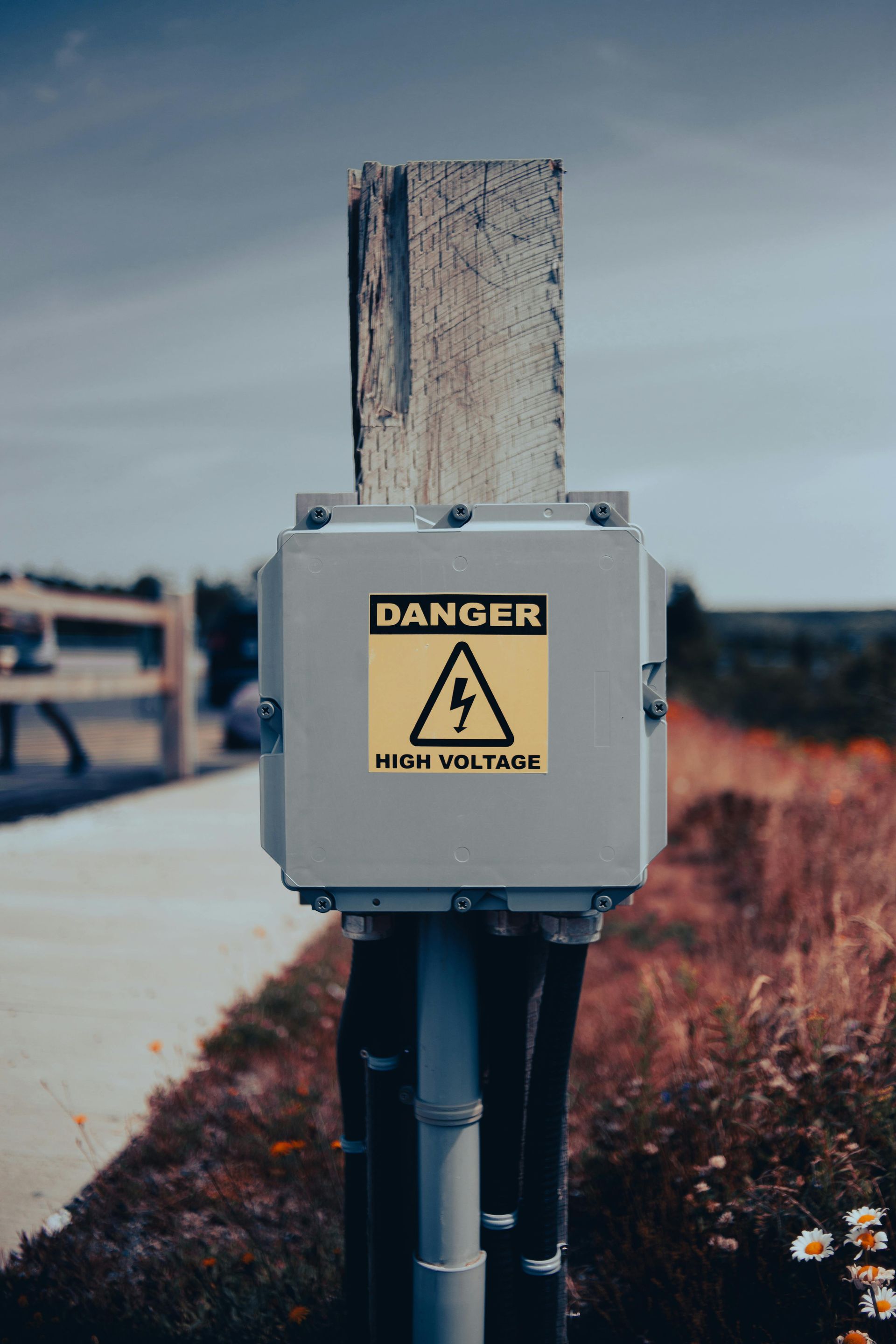
By Swetha Parvathy
•
May 26, 2025
As we increasingly rely on electronic devices and appliances in our daily lives, electrical safety becomes a crucial aspect of home maintenance. Electrical accidents can be devastating, causing injuries, fatalities, and property damage. In this blog post, we'll share essential tips to help you ensure electrical safety at home and avoid electrocution. 1. Keep Water Away from Electricity Water and electricity are a deadly combination. Avoid using electrical appliances near water sources, such as: - Bathrooms - Kitchens - Swimming pools - Outdoor areas during rain or snow 2. Inspect Cords and Appliances Regularly Regular inspections can help identify potential electrical hazards. Check for: - Frayed or damaged cords - Overheating appliances - Sparks or unusual smells - Loose connections or faulty wiring 3. Use GFCIs (Ground Fault Circuit Interrupters) GFCIs are designed to prevent electrical shock by interrupting the power supply when a ground fault occurs. Install GFCIs in areas prone to moisture, such as: - Bathrooms - Kitchens - Outdoor areas 4. Avoid Overloading Outlets and Extension Cords Overloading outlets and extension cords can lead to electrical fires or electrocution. Be mindful of: - Using too many appliances on a single circuit - Overloading extension cords - Using damaged or frayed extension cords 5. Keep Children Safe Children are naturally curious, and electrical safety is crucial for their well-being. Take steps to: - Secure outlets with tamper-resistant covers - Keep electrical appliances out of reach - Teach children about electrical safety 6. Hire a Licensed Electrician For any electrical work, hire a licensed electrician to ensure: - Compliance with local electrical codes - Safe installation and maintenance - Proper diagnosis and repair of electrical issues 7. Be Cautious with Outdoor Electrical Equipment Outdoor electrical equipment, such as generators or power tools, requires special care. Ensure: - Proper grounding and installation - Regular maintenance and inspection - Safe operation and storage 8. Replace Damaged or Outdated Electrical Components Don't hesitate to replace damaged or outdated electrical components, such as: - Old or damaged wiring - Outdated electrical panels - Faulty circuit breakers Conclusion Electrical safety is a critical aspect of home maintenance. By following these tips, you can significantly reduce the risk of electrical accidents and ensure a safe living environment for yourself and your loved ones. Remember, electrical safety is everyone's responsibility.
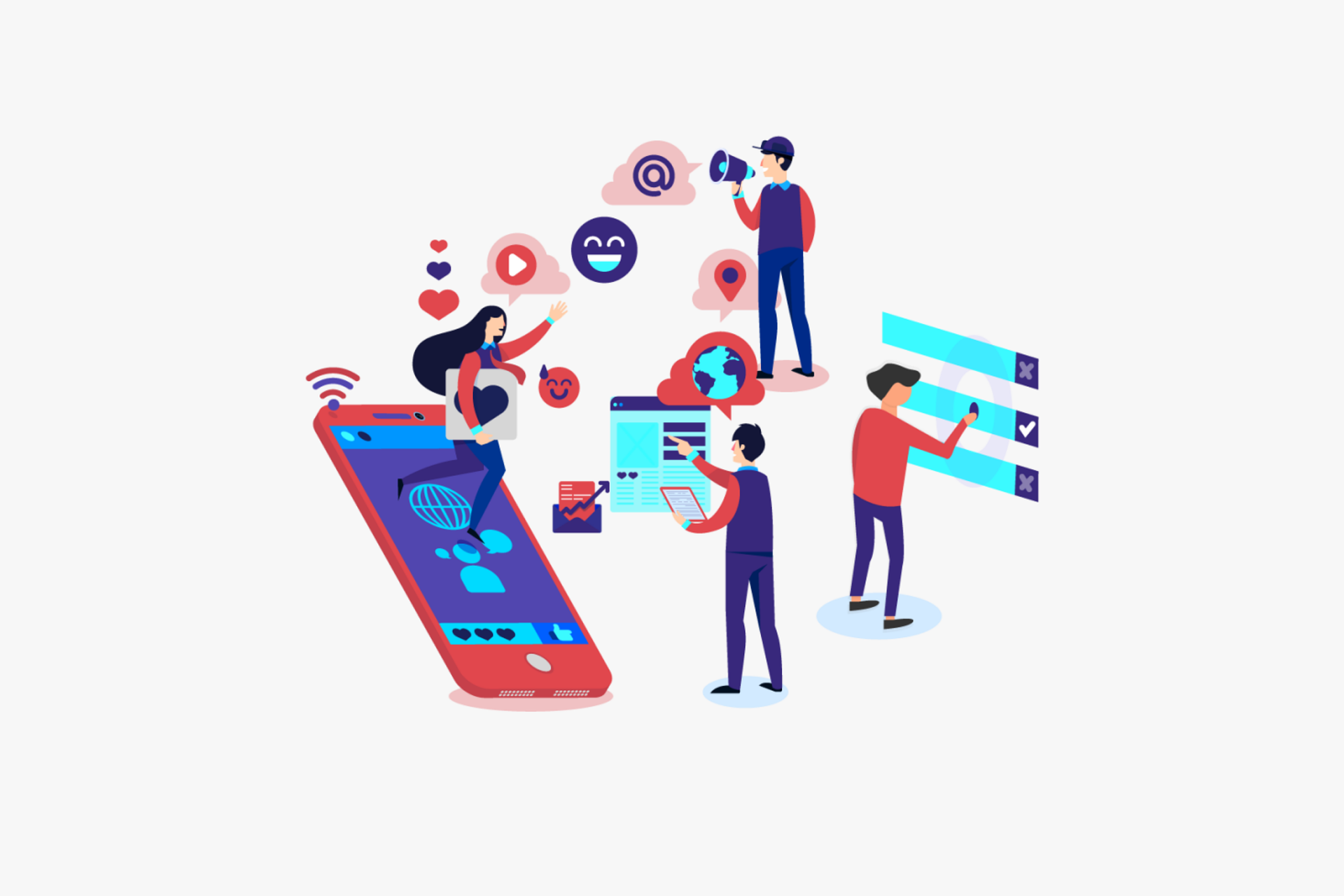
By Swetha Parvathy
•
May 2, 2025
The electronics industry is rapidly evolving, driven by technological advancements and changing consumer needs. Here are some emerging trends that are set to shape the future: 1. The Rise of Electric Vehicles Electric vehicles (EVs) are gaining popularity, driven by environmental concerns and government incentives. EVs offer a cleaner, more sustainable alternative to traditional gasoline-powered vehicles. Key developments in the EV space include: - Advancements in Battery Technology: Improved battery life, range, and charging speed are making EVs more practical for everyday use. - Expansion of Charging Infrastructure: Governments and companies are investing in charging infrastructure, making it easier to own and use an EV. - Increased Model Options: More automakers are launching EV models, offering consumers a wider range of choices. 2. Advancements in Printed Electronics Printed electronics involve using printing techniques to create electronic devices and components. This technology has the potential to revolutionize various industries, including: - Wearable Technology: Printed electronics can be used to create flexible, wearable devices that track vital signs and monitor health. - Flexible Displays: Printed electronics can enable the creation of flexible displays that can be used in a variety of applications, from smartphones to wearables. - Biomedical Devices: Printed electronics can be used to create implantable devices that monitor and treat medical conditions. 3. 3D Printing Technologies 3D printing, also known as additive manufacturing, is transforming the way we design and produce products. Key developments in 3D printing include: - Increased Speed and Accuracy: Advances in 3D printing technology are enabling faster and more accurate production of complex parts and products. - New Materials and Applications: Researchers are developing new materials and applications for 3D printing, including biomedical devices and aerospace components. - Customization and Personalization: 3D printing enables the creation of customized products tailored to individual needs and preferences. Conclusion These emerging trends are set to shape the future of the electronics industry, enabling new applications, products, and experiences. As technology continues to evolve, we can expect even more exciting developments in the years to come.
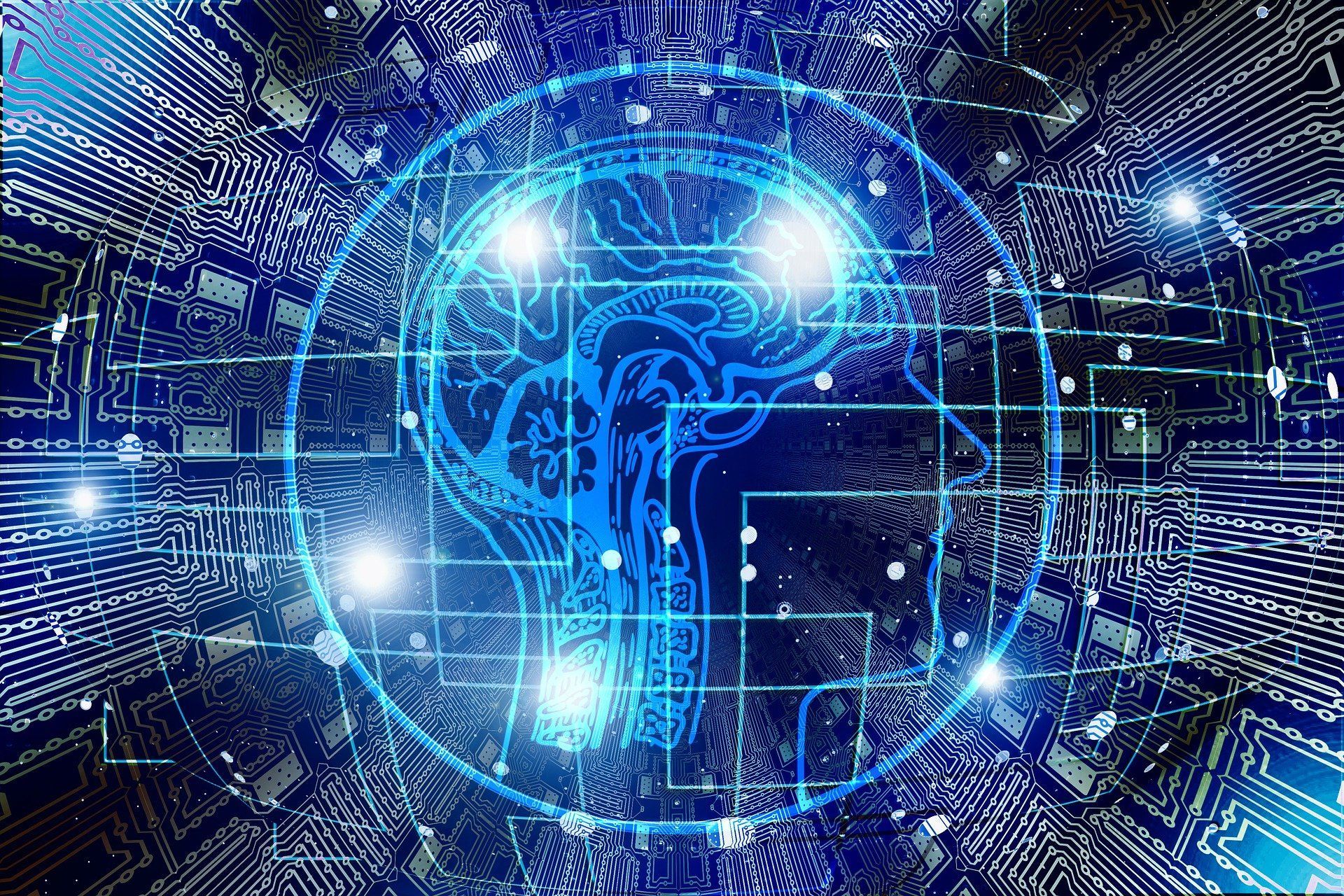
By Anil Arekapudi
•
March 21, 2025
The Evolution of Automotive Electronics: Trends and Advancements The automotive industry has undergone significant transformations over the years, and one of the key drivers of this change has been the rapid evolution of automotive electronics. From simple radio systems to complex advanced driver-assistance systems (ADAS), electronics have become an integral part of modern vehicles. In this blog, we'll explore the trends and advancements that are shaping the future of automotive electronics. The Early Days of Automotive Electronics The first electronic systems in vehicles were introduced in the 1950s and 1960s, with the advent of radio systems, heaters, and basic ignition systems. These early systems were relatively simple and consisted of a few discrete components. The Rise of Microcontrollers and Engine Control Units (ECUs) The 1970s and 1980s saw the introduction of microcontrollers and ECUs, which revolutionized the automotive electronics landscape. Microcontrollers enabled the development of more complex systems, such as anti-lock braking systems (ABS) and traction control systems (TCS). The Advent of Advanced Driver-Assistance Systems (ADAS) The 1990s and 2000s witnessed the emergence of ADAS, which rely heavily on advanced electronics and sensors. Systems like adaptive cruise control, lane departure warning, and automatic emergency braking have become increasingly common in modern vehicles. Current Trends and Advancements 1. Electrification and Autonomous Vehicles: The shift towards electric and autonomous vehicles is driving the development of more advanced electronics, including high-performance computing platforms and sophisticated sensor systems. 2. Connectivity and IoT: The increasing demand for connected cars and IoT-enabled vehicles is driving the adoption of advanced wireless communication technologies, such as 5G and Wi-Fi. 3. Artificial Intelligence and Machine Learning: AI and ML are being increasingly used in automotive electronics to enable advanced features like predictive maintenance, driver monitoring, and personalized infotainment. 4. Cybersecurity: As vehicles become more connected and reliant on electronics, cybersecurity is becoming a major concern. Automotive manufacturers are investing heavily in developing robust cybersecurity measures to protect against hacking and other threats. Future Outlook The future of automotive electronics looks promising, with emerging trends like: 1. Vehicle-to-Everything (V2X) Communication: Enables vehicles to communicate with other vehicles, infrastructure, and pedestrians. 2. Augmented Reality and Virtual Reality: Enhances the driving experience with immersive and interactive displays. 3. Quantum Computing: Enables faster and more secure processing of complex data. In conclusion, the evolution of automotive electronics has been remarkable, and the future looks even more exciting. As technology continues to advance, we can expect to see even more innovative and sophisticated electronic systems in vehicles.
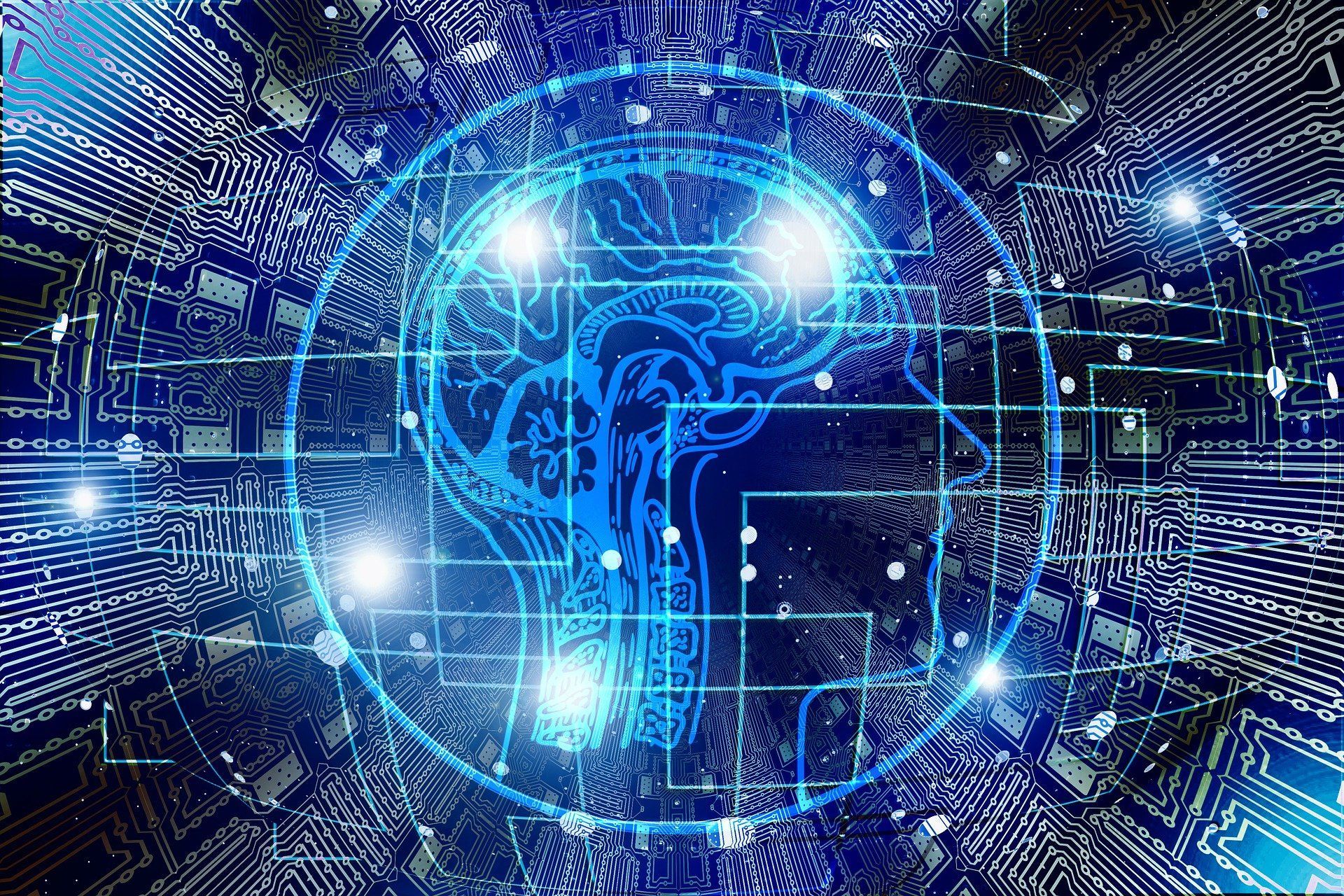
By Swetha Parvathy
•
February 24, 2025
The Internet of Things (IoT) has revolutionized the way we live and work, connecting billions of devices and transforming industries. As we look to the future, it's clear that IoT will continue to play a major role in shaping our world. In this blog, we'll explore the top trends and predictions for the IoT industry over the next five years. Trend 1: Increased Adoption of Edge Computing Edge computing is a distributed computing paradigm that brings data processing closer to the source of the data, reducing latency and improving real-time decision-making. As IoT devices become more widespread, edge computing will become increasingly important for processing the vast amounts of data generated by these devices. Trend 2: Growing Importance of Artificial Intelligence (AI) and Machine Learning (ML) AI and ML will play a crucial role in the future of IoT, enabling devices to learn from their environment and make decisions autonomously. This will lead to increased efficiency, productivity, and innovation across various industries. Trend 3: Expansion of IoT into New Industries IoT is no longer limited to traditional industries like manufacturing and logistics. Over the next five years, we can expect to see IoT adoption in new industries such as: - Healthcare: IoT will enable remote patient monitoring, personalized medicine, and improved healthcare outcomes. - Agriculture: IoT will optimize crop yields, reduce waste, and improve supply chain efficiency. - Smart Cities: IoT will enable cities to become more efficient, sustainable, and livable. Trend 4: Increased Focus on Security and Privacy As IoT devices become more ubiquitous, security and privacy concerns will become increasingly important. We can expect to see a greater emphasis on secure-by-design principles, encryption, and secure data storage. Trend 5: Advancements in Wireless Communication Technologies Wireless communication technologies like 5G, Wi-Fi 6, and Bluetooth 5 will continue to evolve, enabling faster data transfer rates, lower latency, and greater connectivity. Prediction 1: IoT Devices Will Exceed 50 Billion by 2025 The number of IoT devices is expected to grow exponentially over the next five years, driven by increasing demand for smart home devices, wearables, and industrial IoT solutions. Prediction 2: IoT Will Drive Business Model Innovation IoT will enable new business models, such as product-as-a-service, data-driven services, and subscription-based models. Companies that adopt IoT will need to rethink their business strategies to remain competitive. Prediction 3: IoT Will Improve Sustainability and Reduce Carbon Footprint IoT will play a critical role in reducing carbon emissions and improving sustainability. By optimizing energy consumption, reducing waste, and improving supply chain efficiency, IoT will help companies meet their sustainability goals. Conclusion The future of IoT is exciting and rapidly evolving. Over the next five years, we can expect to see increased adoption of edge computing, AI, and ML, as well as expansion into new industries. As IoT continues to transform industries and improve our lives, it's essential to stay informed about the latest trends and predictions. By doing so, we can unlock the full potential of IoT and create a more connected, efficient, and sustainable world.
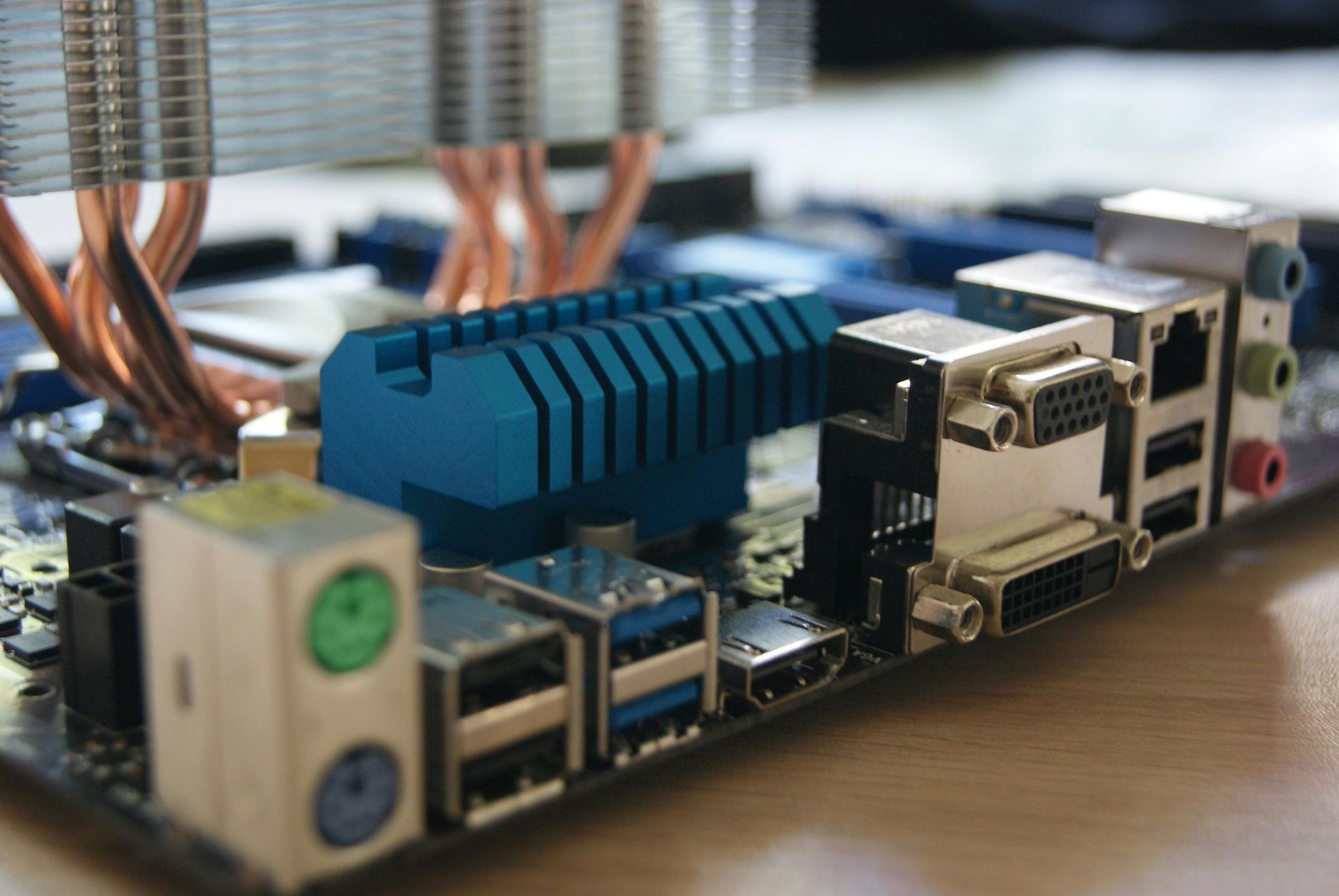
By Swetha Parvathy
•
February 13, 2025
Inductors are a crucial component in electronic circuits, playing a vital role in filtering, impedance matching, and energy storage. With so many types of inductors available, selecting the right one for your circuit can be a daunting task. In this guide, we'll walk you through the key factors to consider when choosing an inductor, helping you make an informed decision for your design. Understanding Inductor Types Before diving into the selection process, it's essential to understand the different types of inductors available: 1. Air Core Inductors: These inductors have no magnetic core and are often used in high-frequency applications. 2. Ferrite Core Inductors: Ferrite core inductors use a magnetic core to increase inductance and are commonly used in power supplies and filters. 3. Iron Core Inductors: Iron core inductors use a magnetic core made of iron and are often used in high-current applications. 4. Toroidal Inductors: Toroidal inductors have a doughnut-shaped core and are used in applications where a high inductance value is required. 5. Chip Inductors: Chip inductors are surface-mount devices that offer high inductance values in a small package. Key Factors to Consider When selecting an inductor, consider the following factors: 1. Inductance Value: Choose an inductor with the correct inductance value for your application. Inductance values range from a few nanohenries (nH) to several henries (H). 2. Current Rating: Select an inductor that can handle the maximum current required by your circuit. 3. Frequency Range: Choose an inductor that operates within the frequency range of your application. 4. DC Resistance: Consider the DC resistance of the inductor, as it can affect the overall efficiency of your circuit. 5. Physical Size: Select an inductor that fits within the physical constraints of your design. 6. Temperature Range: Choose an inductor that operates within the temperature range of your application. 7. Cost and Availability: Consider the cost and availability of the inductor, as well as any potential lead-time issues. Additional Considerations 1. Saturation Current: Be aware of the saturation current of the inductor, as it can affect the overall performance of your circuit. 2. Shielding: Consider the shielding requirements of your inductor, as it can affect the overall electromagnetic compatibility (EMC) of your design. 3. Mounting: Select an inductor with a suitable mounting option, such as through-hole or surface-mount. Conclusion Choosing the right inductor for your circuit requires careful consideration of several factors. By understanding the different types of inductors available and considering key factors such as inductance value, current rating, and frequency range, you can select the optimal inductor for your design. Remember to also consider additional factors such as saturation current, shielding, and mounting to ensure the best possible performance. Recommended Products - Ferrite Core Inductors: Our ferrite core inductors offer high inductance values and are suitable for a wide range of applications. - Chip Inductors: Our chip inductors are surface-mount devices that offer high inductance values in a small package. - Toroidal Inductors: Our toroidal inductors have a doughnut-shaped core and are used in applications where a high inductance value is required.
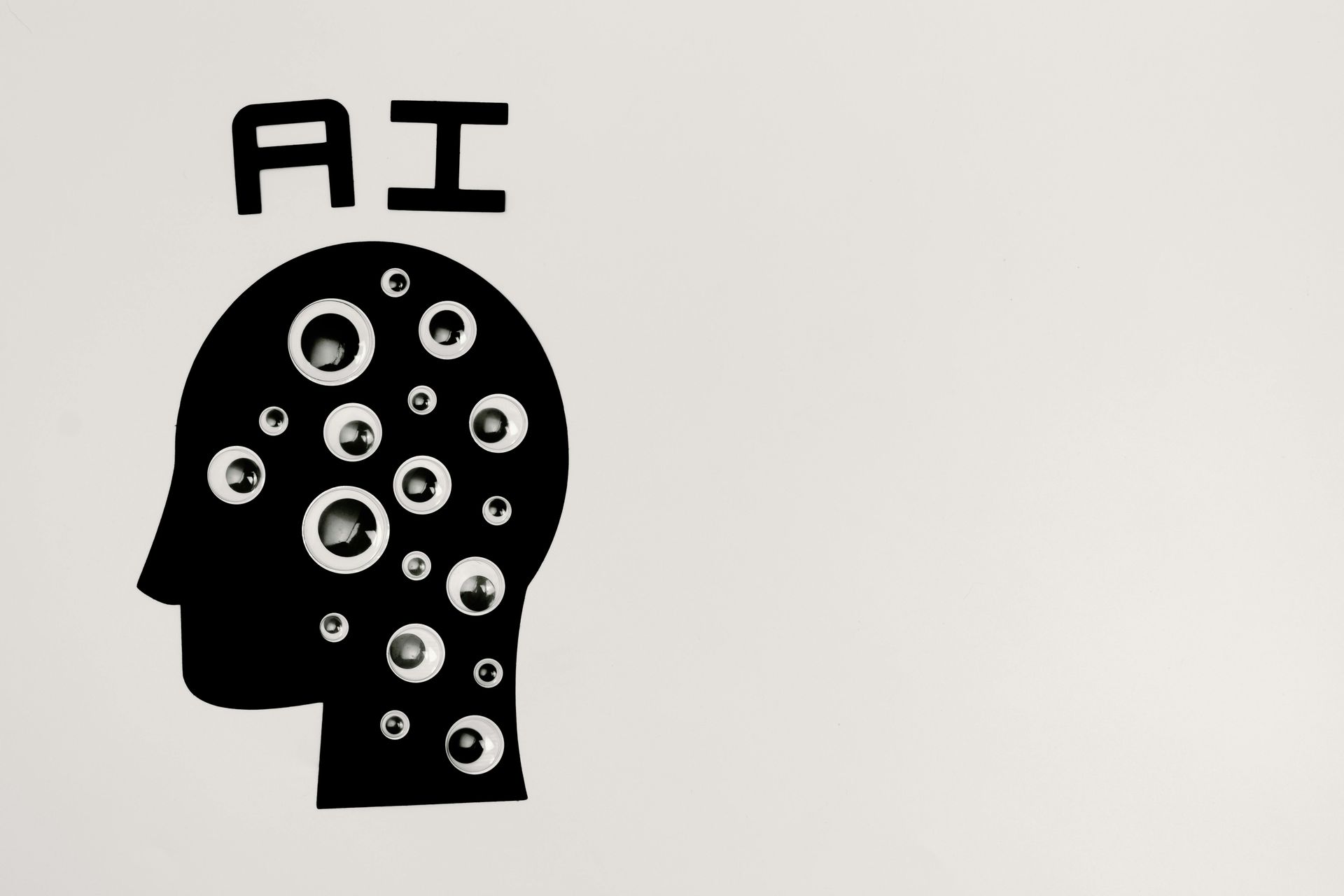
By Swetha Parvathy
•
January 29, 2025
Artificial intelligence (AI) has come a long way since its inception, transforming industries and revolutionizing the way we live and work. As we step into a new decade, it's exciting to think about what the future holds for AI. In this blog, we'll explore the latest trends and predictions that will shape the future of artificial intelligence. Trend 1: Increased Adoption of Edge AI Edge AI refers to the deployment of AI algorithms on edge devices, such as smartphones, smart home devices, and autonomous vehicles. This trend is driven by the need for faster processing, reduced latency, and improved security. As edge AI continues to advance, we can expect to see more intelligent devices that can operate independently, without relying on cloud connectivity. Trend 2: Rise of Explainable AI (XAI) As AI becomes more pervasive, there's a growing need to understand how AI algorithms make decisions. Explainable AI (XAI) is a subfield of AI that focuses on developing techniques to interpret and explain AI-driven decisions. XAI will become increasingly important in high-stakes applications, such as healthcare, finance, and law. Trend 3: Autonomous Systems Autonomous systems, such as self-driving cars, drones, and robots, will continue to advance in the coming years. These systems will rely on sophisticated AI algorithms to navigate complex environments, make decisions in real-time, and interact with humans. Trend 4: Human-AI Collaboration As AI becomes more integrated into our daily lives, there's a growing recognition of the need for human-AI collaboration. This trend is driven by the realization that AI is not a replacement for human intelligence, but rather a complement to it. We can expect to see more AI systems designed to collaborate with humans, augmenting our abilities and enhancing our productivity. Trend 5: AI for Social Good AI has the potential to drive significant social impact, from improving healthcare outcomes to reducing climate change. As AI continues to advance, we can expect to see more applications of AI for social good, including AI-powered disaster response systems, AI-driven medical research, and AI-based environmental monitoring systems. Predictions for the Future of AI 1. AI will become ubiquitous: AI will become an integral part of our daily lives, from smart homes to autonomous vehicles. 2. AI will create new job opportunities: While AI may automate some jobs, it will also create new job opportunities in fields such as AI development, deployment, and maintenance. 3. AI will drive significant social impact: AI will be used to drive significant social impact, from improving healthcare outcomes to reducing climate change. 4. AI will raise important ethical questions: As AI becomes more pervasive, we'll need to address important ethical questions, such as bias in AI decision-making and the potential for AI to exacerbate social inequalities. Conclusion The future of artificial intelligence is exciting and rapidly evolving. As we look ahead to the next decade, it's clear that AI will play an increasingly important role in shaping our world. From edge AI to human-AI collaboration, these trends and predictions offer a glimpse into the future of AI and its potential to drive significant social impact.
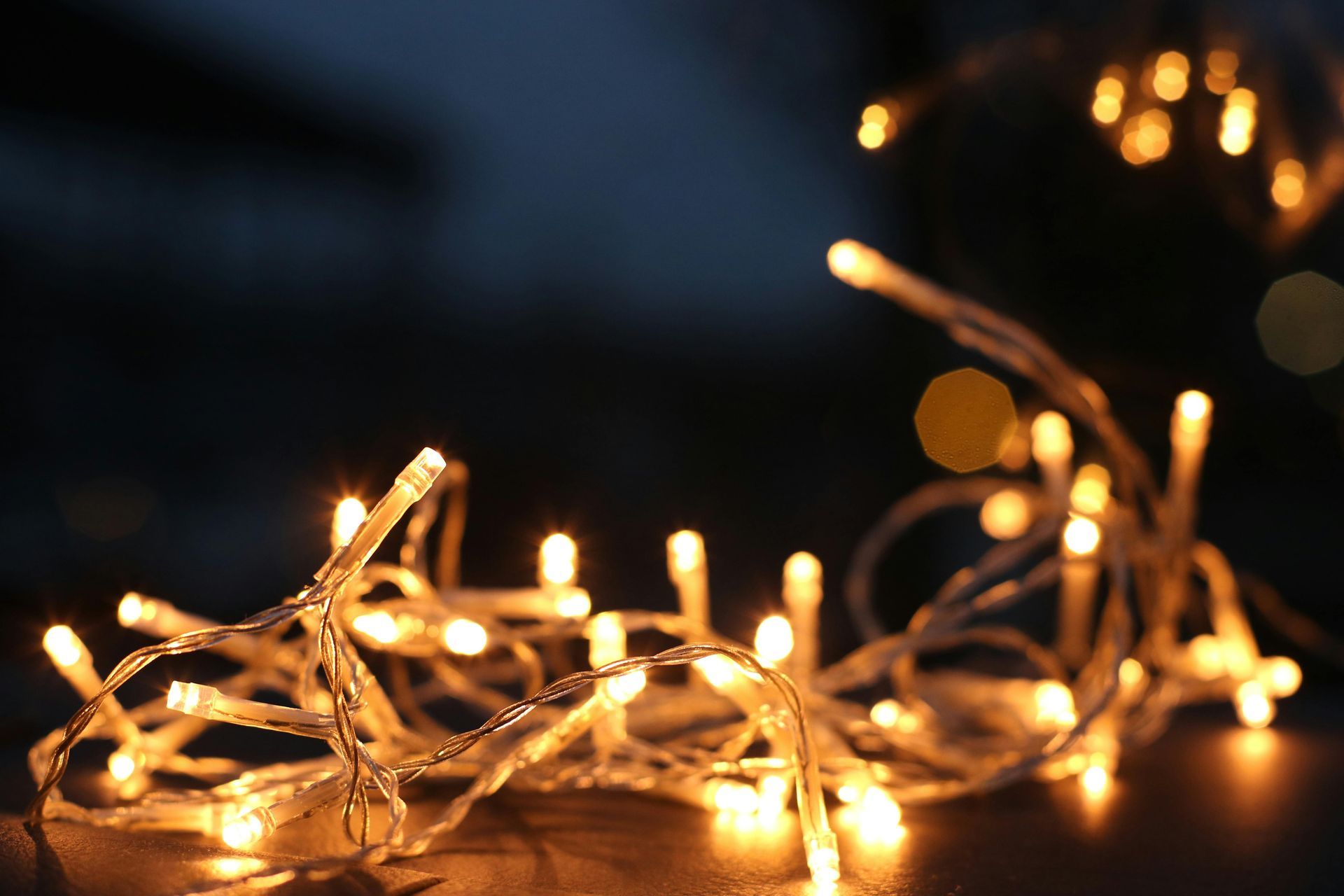
By Swetha Parvathy
•
January 22, 2025
Industrial settings, such as warehouses, manufacturing plants, and construction sites, require reliable and efficient lighting to ensure safety, productivity, and energy efficiency. Traditional lighting options, such as fluorescent and high-intensity discharge (HID) lamps, have been widely used in industrial settings, but they have several drawbacks. LED lighting, on the other hand, offers numerous benefits that make it an attractive alternative for industrial settings. Benefits of LED Lighting in Industrial Settings 1. Energy Efficiency: LED lighting is significantly more energy-efficient than traditional lighting options. LEDs use up to 90% less energy than HIDs and 50% less energy than fluorescent lamps. This can lead to substantial cost savings on energy bills. 2. Longer Lifespan: LEDs have a much longer lifespan than traditional lighting options. They can last up to 50,000 hours or more, compared to 10,000 to 20,000 hours for HIDs and 8,000 to 10,000 hours for fluorescent lamps. This means fewer replacements and reduced maintenance costs. 3. Improved Safety: LEDs are free from toxic chemicals like mercury and lead, which are found in some traditional lighting options. They also produce minimal heat, reducing the risk of burns and fires. 4. Increased Productivity: LEDs can improve visibility and reduce eye strain, leading to increased productivity and reduced errors. They can also be designed to provide specific lighting levels and colors to enhance task performance. 5. Design Flexibility: LEDs offer design flexibility, allowing for a wide range of lighting options, including color temperature, beam angle, and dimming capabilities. 6. Reduced Maintenance: LEDs require minimal maintenance, as they are resistant to shock, vibration, and extreme temperatures. 7. Environmental Benefits: LEDs are an environmentally friendly option, as they are free from toxic chemicals and can be recycled. Industrial LED Lighting Applications 1. Warehouse Lighting: LEDs can provide high-bay lighting for warehouses, reducing energy consumption and improving visibility. 2. Manufacturing Lighting: LEDs can provide task lighting for manufacturing applications, improving productivity and reducing errors. 3. Construction Lighting: LEDs can provide temporary lighting for construction sites, reducing energy consumption and improving safety. 4. Parking Garage Lighting: LEDs can provide energy-efficient lighting for parking garages, improving visibility and reducing energy consumption. Conclusion LED lighting offers numerous benefits for industrial settings, including energy efficiency, longer lifespan, improved safety, increased productivity, design flexibility, reduced maintenance, and environmental benefits. By switching to LED lighting, industrial facilities can reduce energy consumption, improve visibility, and enhance productivity, while also reducing their environmental impact.
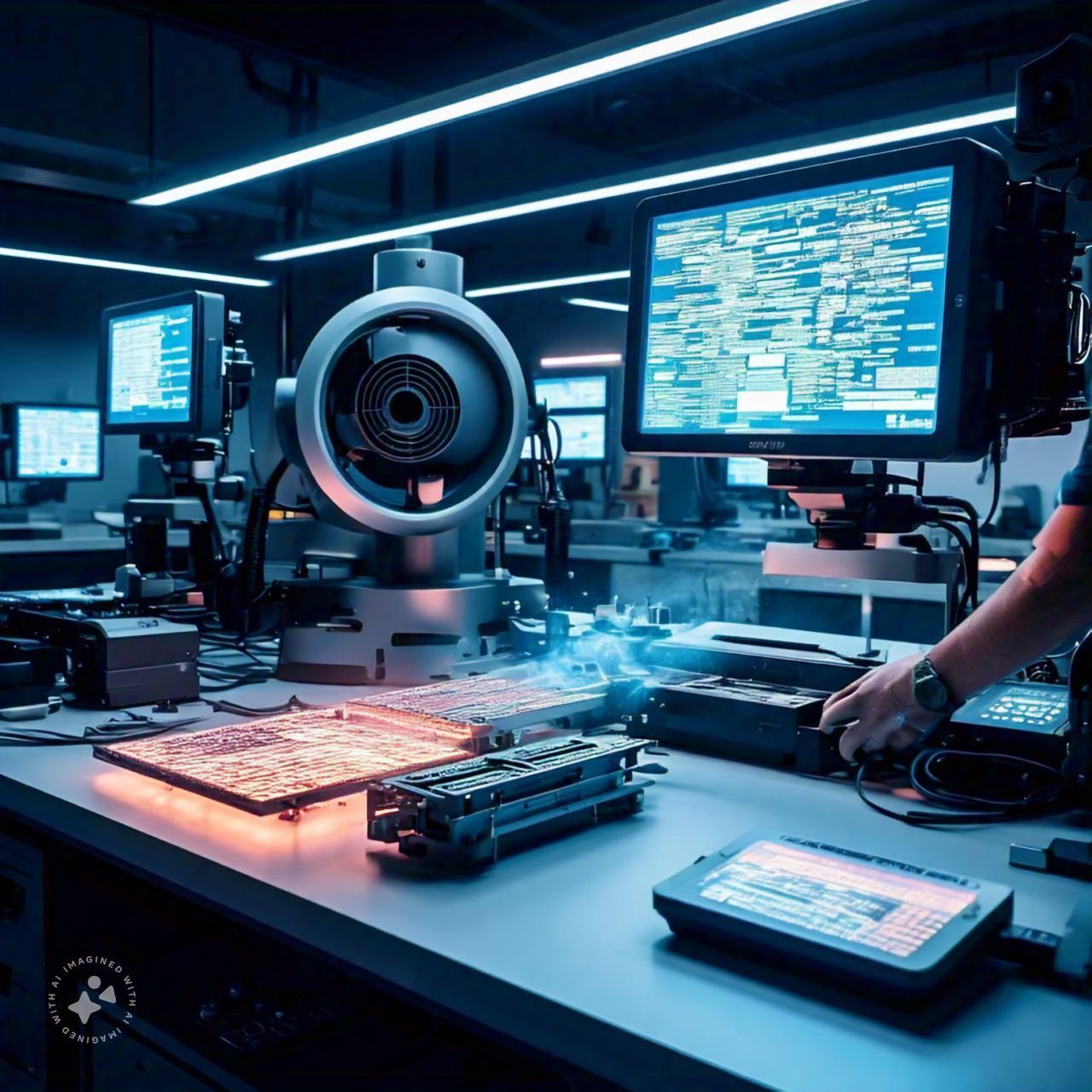
By Swetha Parvathy
•
January 6, 2025
The rapid advancement of electronic devices has led to a significant increase in heat generation, making thermal management a critical aspect of electronics design. As devices become smaller, faster, and more powerful, managing heat effectively is crucial to ensure reliability, performance, and safety. In this blog post, we'll explore the latest trends and best practices in thermal management for electronics, highlighting key strategies and technologies to help you optimize thermal performance and reduce heat-related failures. The Importance of Thermal Management Thermal management is essential in electronics design for several reasons: 1. Reliability: Excessive heat can lead to component failure, reducing the overall reliability of the device. 2. Performance: High temperatures can slow down device performance, affecting processing speed, memory, and overall functionality. 3. Safety: Overheating can cause electrical shocks, fires, or explosions, posing a significant risk to users and surrounding environments. Trends in Thermal Management Several trends are shaping the thermal management landscape: 1. Increased Use of Advanced Materials: New materials like graphene, nanomaterials, and phase-change materials are being explored for their exceptional thermal properties. 2. Integration of Thermal Management into System Design: Thermal management is becoming an integral part of system design, rather than an afterthought. 3. Growing Adoption of Liquid Cooling: Liquid cooling is gaining popularity, particularly in high-performance applications like data centers, gaming PCs, and electric vehicles. 4. Development of Smart Thermal Management Systems: Advanced sensors, algorithms, and control systems are being developed to optimize thermal management in real-time. Best Practices for Thermal Management To ensure effective thermal management, follow these best practices: 1. Conduct Thorough Thermal Analysis: Perform thermal simulations and testing to identify potential hotspots and optimize thermal design. 2. Select Suitable Thermal Interface Materials: Choose materials with high thermal conductivity and suitable mechanical properties. 3. Optimize Heat Sink Design: Design heat sinks with optimal geometry, material, and fin arrangement to maximize heat transfer. 4. Implement Active Cooling Solutions: Use fans, blowers, or liquid cooling systems to actively remove heat from high-temperature components. 5. Monitor and Control Temperature: Implement temperature sensors and control systems to monitor and regulate temperature in real-time. Conclusion Thermal management is a critical aspect of electronics design, and its importance will only continue to grow as devices become more complex and powerful. By staying up-to-date with the latest trends and best practices, you can ensure your devices operate reliably, efficiently, and safely.
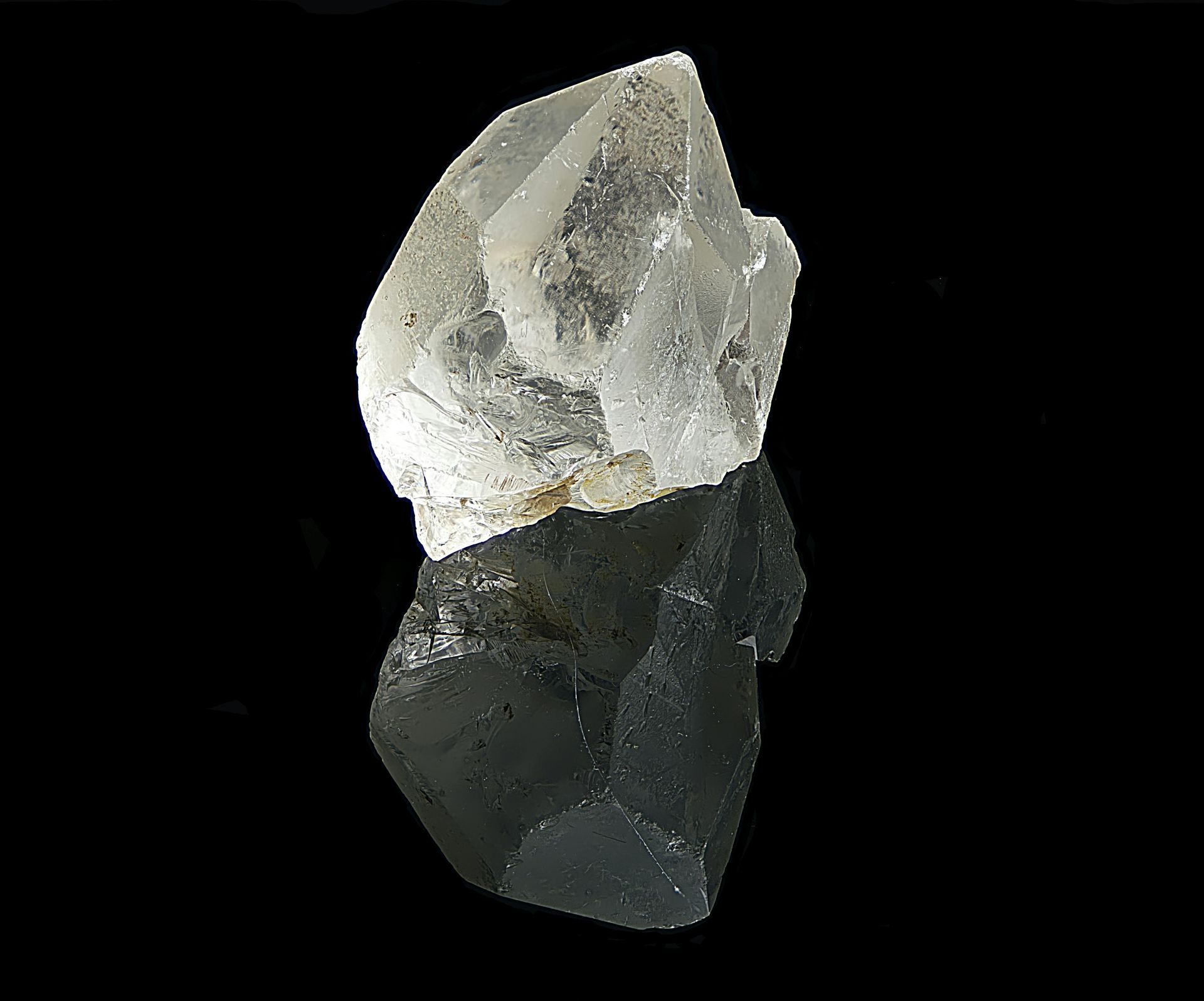
By Swetha Parvathy
•
December 31, 2024
Quartz crystal oscillators (QCOs) have been a crucial component in electronic devices for decades, providing a stable clock signal that enables precise timing and frequency control. From their humble beginnings to the present day, QCOs have undergone significant transformations, driven by advances in materials science, manufacturing techniques, and market demands. In this article, we'll delve into the evolution of quartz crystal oscillators, exploring their past, present, and future. The Early Days: 1920s-1950s The concept of using quartz crystals for frequency control dates back to the 1920s. Researchers discovered that quartz crystals, when excited by an electric current, could produce a stable frequency signal. This phenomenon, known as piezoelectricity, laid the foundation for the development of QCOs. In the 1950s, the first quartz crystal oscillators were introduced, primarily used in military and telecommunications applications. These early QCOs were relatively large, expensive, and prone to frequency drift. The Golden Age: 1960s-1980s The 1960s marked the beginning of the golden age for QCOs. Advances in quartz crystal growth, cutting, and polishing techniques led to improved frequency stability and reduced production costs. This, in turn, enabled the widespread adoption of QCOs in various industries, including consumer electronics, aerospace, and automotive. During this period, QCOs underwent significant design and packaging innovations, such as the introduction of metal packages, surface-mount technology, and voltage-controlled oscillators (VCOs). Modern Era: 1990s-Present The 1990s saw the emergence of new technologies that further transformed the QCO landscape. Some notable developments include: 1. AT-Cut Quartz Crystals: The introduction of AT-cut quartz crystals, which offered improved frequency stability and reduced aging effects. 2. Surface-Acoustic Wave (SAW) Technology: SAW technology enabled the creation of smaller, more stable QCOs with improved frequency accuracy. 3. MEMS-Based QCOs: The development of microelectromechanical systems (MEMS)-based QCOs, which offered enhanced performance, reduced size, and lower power consumption. Today, QCOs are ubiquitous in modern electronics, found in applications ranging from smartphones and laptops to medical devices and industrial control systems. Future Outlook As technology continues to advance, QCOs will likely undergo further transformations. Some potential trends and developments on the horizon include: 1. Increased Integration: Further integration of QCOs with other components, such as microcontrollers and sensors, to create more compact and efficient systems. 2. Advanced Materials: The exploration of new materials and technologies, such as graphene and nanomaterials, to improve QCO performance and reduce size. 3. Wireless and Wearable Applications: The growing demand for wireless and wearable devices will drive the development of smaller, more power-efficient QCOs. 4. IoT and 5G: The proliferation of IoT devices and 5G networks will require QCOs with improved frequency stability, accuracy, and reliability. In conclusion, the evolution of quartz crystal oscillators has been a remarkable journey, marked by significant technological advancements and innovations. As we look to the future, it's clear that QCOs will continue to play a vital role in shaping the electronics landscape. About US Electronics US Electronics is a leading provider of quartz crystal oscillators and other electronic components. With a commitment to quality, innovation, and customer satisfaction, we supply QCOs to a wide range of industries and applications. Contact us today to learn more about our products and services.